Advantages of Investment Casting Vs. Other Metal Forming Processes
The investment casting process competes with the majority of metal forming processes and offers some unique advantages. Read about advantages of investment casting over other metal forming processes – like machining, welding, sand casting, die casting and forging.
Investment Casting Vs. Machining
Milling, turning, drilling, and grinding operations can be replaced by investment casting. The capability of investment casting to achieve near net-shapes significantly reduces and many times can completely eliminate the need for machining. You can achieve faster turnaround for volume production with significantly less labor cost and material waste.
Investment castings are used in many critical applications where non-porous, non-shrinking parts are required as they can meet or exceed the standards of a forging or machined bar stock.
Investment cast valves, for example, are typically less expensive than machining the parts from bar stock. This is due to the high tolerances of investment cast finished parts.
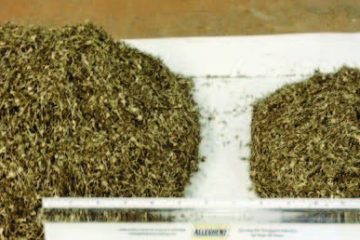
Actual amount of turnings produced by the machining of one set of a 3.5” (8.89 cm) neck ring. Sand cast set on left, investment cast on right.
Investment Casting Vs. Welding
Converting welding applications to investment castings can potentially reduce labor costs, especially with complex components. Labor cost is expended with each increase in the number of joints, the difficulty of the weld, the assembly difficulty, and the number of pieces being joined. In addition to the cost component, investment casting can be advantageous for improved part strength and uniformity, particularly with hard-to-weld alloys. Part appearance is also improved, since there will no longer be visible weld lines as welded and fastened parts can be cast as one piece. Investment casting lends itself to parts that will be higher volume runs, since initial tooling cost may not be suitable for small runs.
Read about the weld conversion of a Trough Mounting Bracket to investment casting. By converting to investment casting, the number of parts were reduced – as well as the weight for more than a 26% reduction in costs! Franklin Precision Castings was awarded Honorable Mention for the 2017 AFS Casting Competition for this job.
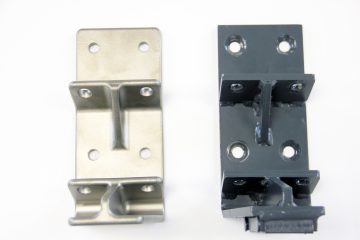
Trough Mounting Bracket converted from welding resulted in reduction of number of parts, weight, and costs – as well as near elimination of machining, superior surface finish and dimensional repeatability and consistency.
Investment Casting Vs. Sand Casting
Due to the nature of the process, investment castings can be held to much tighter tolerances than sand castings or forgings. This can be important and can avoid machining or other finishing operations. Investment casting offers near net-shape, thus reducing costly machining time. Investment casting is also capable of more reliable castings with much thinner walls than sand castings. Due to the thinner wall capability, investment castings produce substantially less scrap rates and lighter weight castings. Investment castings, in general, provide a much higher percentage of defect free-castings.
An example of this is the conversion of neck rings for glass container manufacture from sand to investment casting. The near net shape that is achieved with the neck rings outweigh the costs incurred through the less precise and less efficient process of sand cast.
Investment Casting Vs. Die Casting
In comparison to die casting, investment casting offers a wider range of alloys that can be investment cast, such as stainless steel alloys. Investment castings are also a great alternative for lower production volume projects that are not feasible for die castings due to high tooling costs. Tooling costs for investment castings are much lower, especially when made in-house by Franklin Precision Castings. Die casting also requires more maintenance than investment casting as die castings quickly wear.
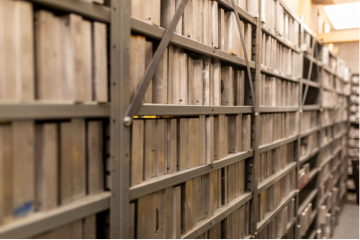
In-house tooling capabilities at Franklin Precision Castings provides the advantage of speed and lower tooling costs
Investment Casting Vs. Forging
Investment casting does not have the expensive tooling costs as seen with forgings. In forged parts, there is also an issue of non-uniform internal stresses and parting lines, neither present with investment cast parts. Forging is also typically a much more expensive metal forming process than investment casting.
Have a part you would like converted to an investment casting?