10 Advantages of Investment Casting
There are many advantages to investment casting which will lead to better design and a lower cost product.
The investment casting process offers many benefits including cost savings, design and material freedom, close tolerances, better finishes, savings in machining time, reproducibility, and overall – they just look better! Read about the 10 advantages of investment casting.
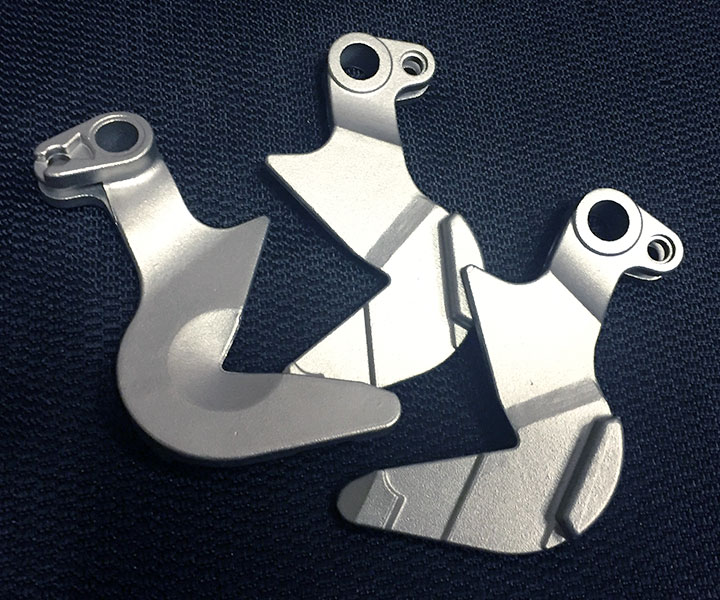
Investment Cast Stainless Steel Pinchers for the Food Industry
1. Superior Surface Finish
The investment casting process provides far superior surface finish as compared to forgings and sand castings. This can be important at times to avoid machining or other finishing operations.
2. Variety of Materials
Investment cast parts can be cast in a range of alloys including stainless steel, brass, bronze, cobalt, nickel and custom alloys. Franklin Precision Castings casts alloys for many applications in a broad range of industries.
3. Closer to Finished Part Designs
Investment castings provide near net shapes for manufactured parts, thus eliminating or reducing machining costs. An added benefit of near net shape is the savings on material, especially with more expensive alloys like nickel and cobalt alloys.
4. Intricate Design
Holes, undercuts, slots and other difficult detail that cannot be had with other processes can often be provided through investment casting – thus reducing the amount of machining. Logos, numbers or names can be incorporated on parts as markings.
5. Difficult Thin Wall Castings
The investment casting process is capable of more reliable castings with much thinner walls than sand castings. Advantages include substantially less scrap rates and castings that weigh less due to the thinner wall capability.
6. Tight Tolerances
Due to the nature of the process, investment castings can be held to much tighter tolerances than sand castings or forgings. Tolerances down to + – 0.1mm can be achieved – resulting in a highly accurate cast part.
7. Competitive Tooling Costs
With Franklin Precision Castingss’ own in-house tool manufacturing, initial charges for the investment casting tooling are often less expensive than those for die castings and forgings.
8. Minimal Casting Defects
Being a cleaner process than sand moulds, investment castings in general, provide a much higher percentage of defect free-castings.
9. Rapid Prototyping for New Product Development
Rapid prototyping can get products to market faster. Franklin Precision Castings uses 3-D Wax Modeling for efficiency and speed in design and production. Using 3-D Modeling, Franklin Precision Castings can move faster from the development phase to the production phase. 3-D Modeling can be especially beneficial for those with requiring quick, small order prototyping as there is no need for wax model tooling. This speed to market helps customers compete in the marketplace.
10. And…they just look better!
Whether or not appearance is critical, investment castings have the appearance of high quality. Minimal to no discernible parting lines are the norm. Also, most outside surfaces do not require draft.
Have a part you want to investment cast?