Bring Your Concepts to Life
Franklin’s in-house capabilities allow us to handle proof-of-concept parts and 3D drawings seamlessly, working closely with your team to optimize casting designs for ideal metallurgy and geometry.
From rapid prototyping to first-article approval, our process delivers swift turnaround times, precise results, and lasting confidence in your casting designs.
Many customers come to us with specific requirements that rapid prototype casting can address, such as:
- Requirement for a physical casting to test a prototype assembly.
- The volume demand for castings does not justify the cost to manufacture tooling.
- Limited time (wax patterns can be cast quickly) .
- Need to optimize part design in coordination with foundry friendly geometries to ensure lower manufacturing cost without sacrificing quality.
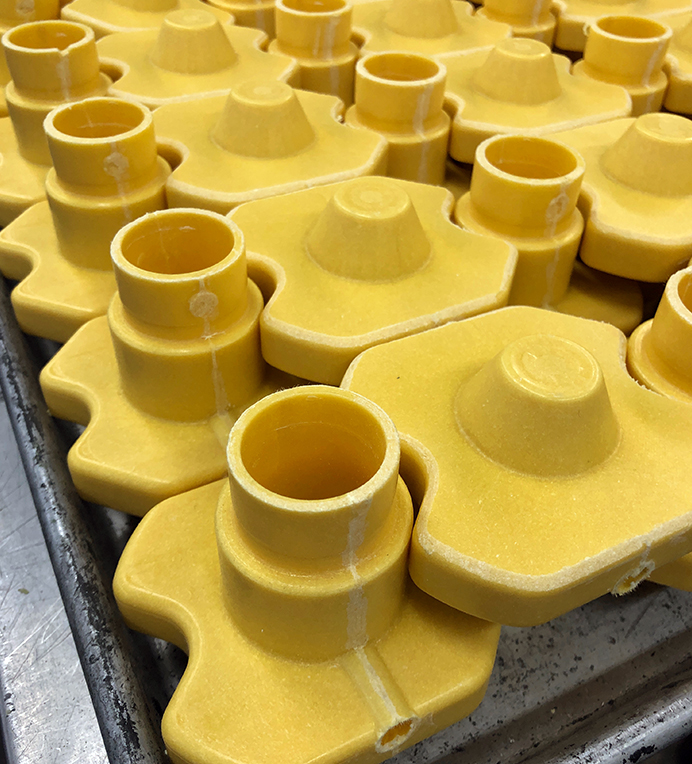
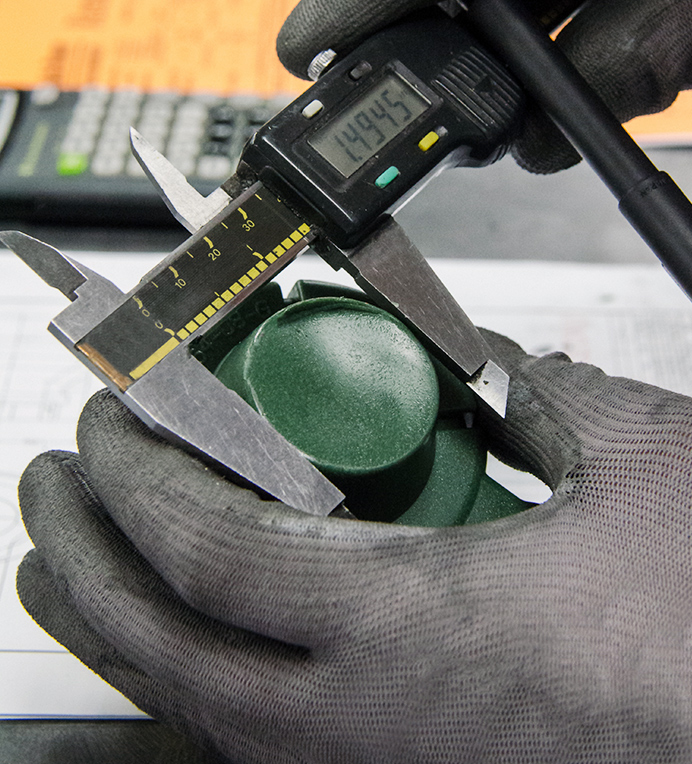
Advantages of Rapid Prototype Casting
- Significant reduction in lead times
- Accelerated product development cycle
- Minimized costs associated with design changes later in the production process
- Creation of highly detailed and accurate prototypes that closely match the final parts
- Material flexibility that allows for testing of various alloys and properties
- Ability to quickly produce and test multiple iterations of prototypes
- Enables rapid design refinements that ultimately lead to superior final products
Why Franklin for Rapid Prototype Casting?
Franklin's rapid prototype casting process provides fast, cost-effective, and precise metal prototypes, empowering engineers to innovate with confidence and efficiency.
Alloys We Pour
We pour over 120 alloys in our U.S.-based facility, including standard and custom stainless steel, nickel, cobalt, brass, bronze, and Ni-Hard alloys to suit the requirements of complex cast subassemblies or assemblies.