Precision. Quality. Reliability.
The Franklin team began investment casting production in 1985 and has since grown into one of the leading automated investment casting foundries in the U.S. With our onsite tooling team, automated casting foundry, and CNC machine shop, we enable faster turnaround times without compromising quality.
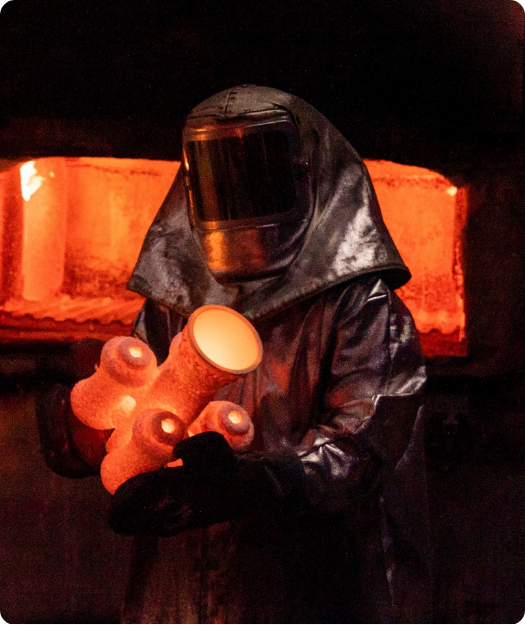
Advantages of Investment Casting
- Superior surface finish and dimensional repeatability
- Tight tolerances and zero to minimal draft angle
- Fine detail reproduction
- Produce to near net shape
- Reduction/elimination of machining
- Ability to cast complex geometries
- Capable of casting thin wall castings
- Range of alloys and casting sizes
- Inexpensive wax tooling
- Recyclable raw materials (ex. wax and ceramic shell molds)
Why Franklin for Investment Castings?
The Franklin team accepts every challenge head-on, working closely together to turn complexity into craftsmanship on a daily basis. With a can-do attitude permeating every corner of our foundry, we’re able to embrace even the most unique requests while delivering exceptional results – every time.
Alloys We Pour
We pour over 120 alloys in our U.S.-based facility, including standard and custom stainless steel, nickel, cobalt, brass, bronze, and Ni-Hard alloys to suit the requirements of complex cast subassemblies or assemblies.