Stainless Steel Investment Casting vs Weldment
Franklin Precision Castings worked with a customer to convert its welded Trough Mounting Bracket to a stainless steel investment casting – reducing weight, simplifying logistics, improving quality, cutting costs, and supporting customers’ requirements.
Converting welding applications to investment castings can potentially reduce labor costs, especially with complex components. Labor cost is expended with each increase in the number of joints, the difficulty of the weld, the assembly difficulty, and the number of pieces being joined. In addition to the cost component, investment casting can be advantageous for improved part strength and uniformity, particularly with hard-to-weld alloys. Part appearance is also improved, since there will no longer be visible weld lines as welded and fastened parts can be cast as one piece. Investment casting lends itself to parts that will be higher volume runs, since initial tooling cost may not be suitable for small runs.
By converting the Trough Mounting Bracket from weldment to a stainless steel investment casting, the number of parts was reduced – as well as the weight for more than a 26% reduction in costs! Franklin Precision Castings was awarded Honorable Mention for the 2017 AFS Casting Competition for this weld conversion.
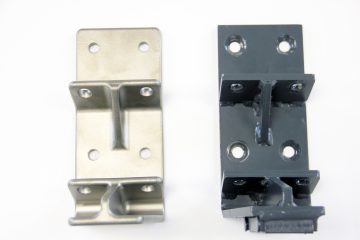
Trough Mounting Bracket converted from welding resulted in reduction of number of parts, weight, and costs – as well as near elimination of machining, superior surface finish and dimensional repeatability and consistency.
Application
Trough Mounting Bracket – A structural part used in vibratory material handling unit for pharmaceuticals, food handling, small parts manufacture, and bulk material movement.
The application is a bracket that supports a trough in a vibratory material handling unit. Underneath this unit is the Vibratory In-Line Drive. The Trough Mounting Bracket is a key part of the Vibratory In-Line Drive. It is assembled to the trough above with bolts, and is joined by welding to the armature (another part of the Drive). These units vibrate at 3600 cycles per minute. They are used in applications like pharmaceuticals, food handling, small parts manufacture, and bulk material movement.
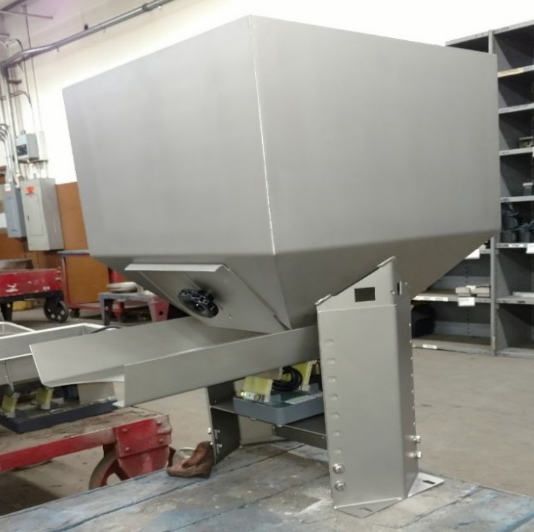
Bulk Supply Hopper used in material handling.
Weldment Conversion to a Stainless Steel Investment Casting
The original trough mounting bracket was fabricated from carbon steel or stainless steel bar stock and then machined. The welded parts suffered from problematic dimensional repeatability.
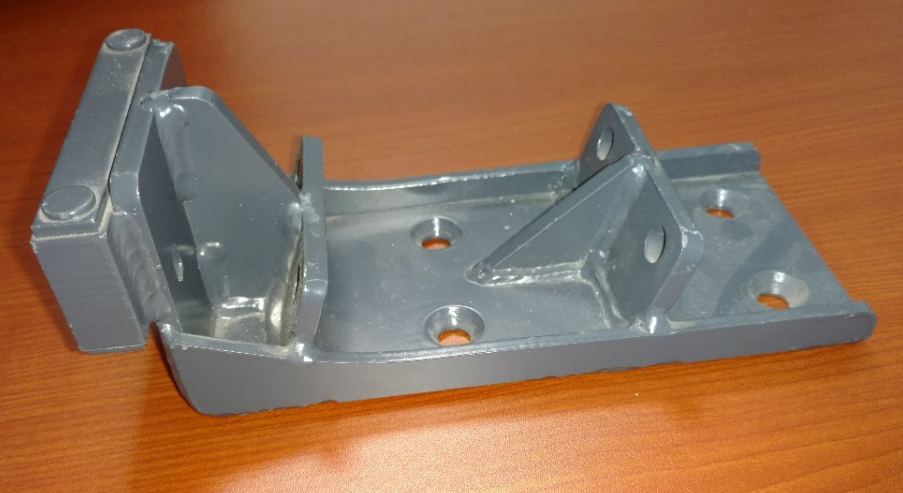
Trough Mounting Bracket shown as a mild carbon steel weldment, machined and painted.
Engineered metal components often start as weldments. This is because welding a single prototype is a low cost solution as no tooling is required. The weldment is usually subsequently machined because machined tolerances are much more precise than those achievable with a plain weldment. The cost advantage of welding is mostly kept to prototyping phase or short runs.
As a part matures from prototype to short run to full production, part volumes start to rise. Rising volumes open the door to metal casting. Specifically, with rising volumes, the cost of foundry tooling can be amortized over more and more.
Originally, two versions were offered for the Bracket. The original Trough Mounting Bracket was fabricated from mild carbon steel, machined and painted. The other was made in welded SAE 304 stainless steel stock, which is demanded by the food and pharmaceutical industries for safe food handling and health regulations, and subsequently machined as well.
The part demanded dimensional repeatability and consistency. The top surface had to be flat, and the angular flanges had to be at the correct angle. The hole locations and the key dimensions had to be exact, and if not, the unit would not operate properly. The welded parts could not produce the required dimensional repeatability and consistency. The rising prices for welding and subsquent machining compelled the customer’s purchasing department to seek alternate manufacturing methods to control costs by creating a near net shape earlier in the process. Investment casting is inherently a shaping or metal forming process, so a good casting design will minimize or eliminate the need for welding and machining the component.
Results when converted to Stainless Steel Investment Casting:
- Reduced Part Count from 9 to 1
- Reduced Weight by 32%
- Reduced Costs by 26%
- Nearly Eliminated Machining
- Superior Surface Finish and elimination of process step – No painting operation needed / Produced a better looking part
- Dimensional repeatability and consistency – tighter dimensional tolerances
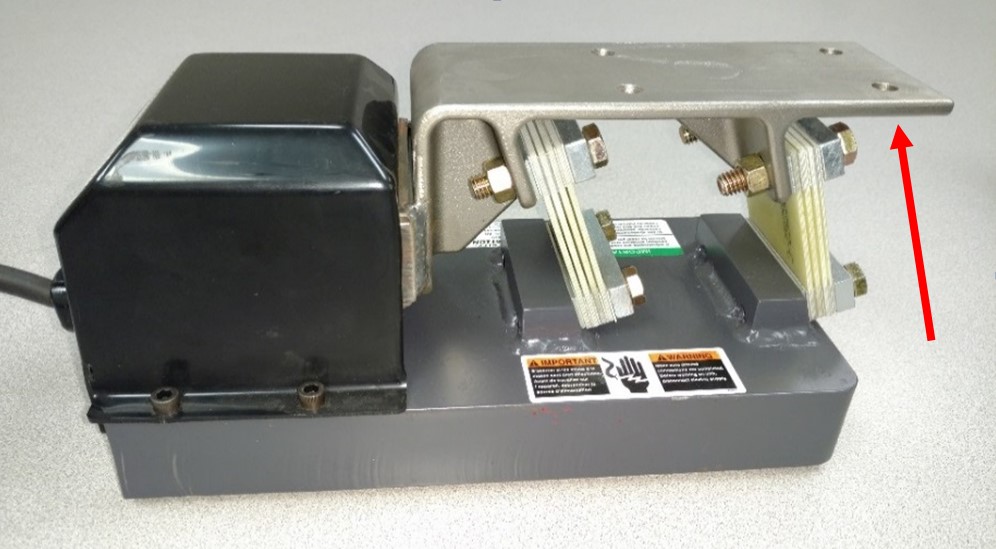
Vibratory In-Line Drive. Arrow indicates Trough Mounting Bracket. Shown as a Stainless Steel Investment Casting.
Ready to discuss your weld part as an investment casting?